The Launch tower team has been working very hard this semester to come up with a good design that will be able to withstand all the forces and safety constraints for our rocket launch. Here’s some details on their design as well as information about their prototype for this semester. Check it out!
Here is our current design for the launch tower. Right now the tower is 25 feet tall. We are planning to construct the tower out of one-inch steel pipe. We chose steel for its strength and for the ease of welding.
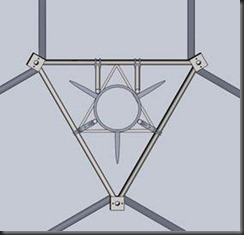
As you can see from the top view of the launch tower, there is a system of rails that support the tower and run in direct contact with the length of the rocket. We wanted to know how much force the rails are going to feel and how much force they could take.
The first test we performed was to find the coefficient of friction between the rails and the rocket. We used a simple force gauge to measure and then calculate the coefficient of friction. We found the coefficient of friction of be about .20.
Then we built a section of the launch tower and tested it in the load frame. The section of tower we built sustained about 425 pounds of force. So, if the rails supported the rocket with a 10-pound compressive force, it would translate to a 2-pound upward force on the rails. Or in other words the launch tower is not going to fail in this way.
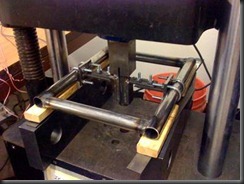